Il mercato vuole prodotti personalizzati con tempi e prezzi equivalenti allo standard
La variety reduction è la metodologia per rispondere con efficacia ed efficienza al mercato
PREMESSA
Le aziende che producono prodotti con personalizzazioni dovute a richieste dei clienti sono sempre più soggette alle esigenze contrastanti di dover rispondere a tali richieste con tempi di sviluppo ridotti il più possibile e anche con costo del prodotto paragonabile a quello senza personalizzazioni.
Si possono individuare due percorsi che rispondono a queste esigenze:
- una efficace pianificazione della progettazione e, a seguire, della produzione
- ottimizzazione delle varianti del prodotto in ottica di “variety reduction”,
La prima è normalmente seguita nelle Aziende, perché ritenuta più pronta per rispondere alle esigenze del cliente, ma gestendo il singolo prodotto solo in ottica di riduzione tempi, questo porta a costi più elevati, in quanto si creano sempre nuovi codici. Sebbene l’effetto complessivo possa essere una riduzione dei tempi, l’aumento dei codici da gestire crea comunque dei tempi di realizzazione più lunghi, compensati dalla migliore pianificazione.
La seconda invece si propone di ridurre il numero dei codici creando gruppi base eguali cui applicare con facilità le personalizzazioni: si deve subire un costo alto per creare il sistema, ma successivamente si hanno costi bassi di personalizzazione e tempi più rapidi per la costruzione del nuovo prodotto.
Resta comunque evidente che la sola applicazione del secondo metodo che porta benefici in termini di costi e tempi, deve comunque essere accompagnata ad una efficace pianificazione, altrimenti tali benefici andrebbero in parte dispersi.
COME OPERARE
I due percorsi partono dall’analisi dello storico:
Sebbene molti prodotti sono stati realizzati su specifica del cliente, è senz’altro possibile suddividerli in base alla tipologia di funzioni e prestazioni che possiedono. Pertanto il primo passo è la creazione di un organigramma di prodotto che individui le famiglie di prodotti, quindi di prodotti che svolgono funzioni simili, ma con prestazioni differenti.
PIANIFICAZIONE
A – primo percorso
Ogni prodotto di ciascuna famiglia avrà una parte standard e una parte personalizzata in base alle richieste del cliente. Il livello di personalizzazione può essere più o meno elevato e questo comporterà un tempo più o meno lungo di sviluppo del progetto, sia meccanico che elettronico comprensivo del software. A seguire la realizzazione dei particolari meccanici, il montaggio e il collaudo saranno più o meno complicati con tempi che si allungano in caso di personalizzazioni sempre più spinte.
È quindi necessario che l’azienda abbia un sistema di consuntivazione delle ore che permetta di sapere i vari tempi di realizzazione del prodotto (progettazione meccanica ed elettronica, produzione particolari, montaggio e collaudo). Senza un sistema di consuntivazione delle ore per prodotto diventa molto complicato fare una stima attendibile dei tempi di sviluppo di un nuovo prodotto.
Raccolti i dati a consuntivo delle ore impiegate per lo sviluppo si possono fare delle tabelle di tempi considerando per lo stesso prodotto se la personalizzazione richiesta è bassa, moderata o molto alta.
A seconda del grado di complessità aumenta il monte ore necessario per completare progettazione e a seguire produzione e collaudo. Si possono così creare delle tabelle tipo le seguenti:
Progettazione meccanica | ||||
Famiglia prodotti | Prodotto | Personalizzazione bassa (ore) | Personalizzazione media (ore) | Personalizzazione alta (ore) |
Famiglia prodotto tipo 1 | Prodotto 1.1 | 40 | 80 | 120 |
Prodotto 1.2 | 50 | 100 | 150 | |
……. | ||||
Famiglia prodotto tipo 5 | Prodotto 5.1 | 70 | 150 | 250 |
Progettazione elettronica | ||||
Famiglia prodotti | Prodotto | Personalizzazione bassa (ore) | Personalizzazione media (ore) | Personalizzazione alta (ore) |
Famiglia prodotto tipo 1 | Prodotto 1.1 | xxx | xxx | xxx |
……. | ||||
Famiglia prodotto tipo 5 | Prodotto 5.1 | xxx | xxx | xxx |
Montaggio | ||||
Famiglia prodotti | Prodotto | Personalizzazione bassa (ore) | Personalizzazione media (ore) | Personalizzazione alta (ore) |
Famiglia prodotto tipo 1 | Prodotto 1.1 | xxx | xxx | xxx |
……. | ||||
Famiglia prodotto tipo 5 | Prodotto 5.1 | xxx | xxx | xxx |
Sulla base del tipo di prodotto richiesto e del grado di personalizzazione, è possibile calcolare in modo abbastanza preciso le ore necessarie a completarlo nelle varie fasi (dalla progettazione al collaudo).
Il project manager in base a date di consegna e risorse disponibili può quindi pianificare la realizzazione del prodotto nei modi più opportuni.
Con una visione di vari mesi delle risorse impegnate in base ai progetti da svolgere, il venditore può avere una buona previsione delle date di consegna e quindi in fase di trattazione di nuovi ordini può gestire la data col cliente.
B – secondo percorso e l’ottimizzazione:
STUDIO DELLE VARIANTI DI PRODOTTO PER LA LORO GESTIONE EFFICACE (VARIETY REDUCTION)
Lo scopo è di creare parti o gruppi comuni a prodotti della stessa famiglia e possibilmente anche ad altre famiglie, che non necessitino di essere progettati e possano essere la base a cui vengono aggiunte le personalizzazioni.
Inoltre anche le personalizzazioni possono essere classificate, in modo da identificare quelle che si sono verificate più volte nelle richieste dei clienti. In questo modo possono essere gestite come gruppi opzionali da aggiungere ai gruppi standard dei singoli prodotti.
Il punto di partenza è sempre l’organigramma di prodotto, ma il lavoro deve procedere per famiglia.
Dato che si parla di prodotti della stessa famiglia è necessario scomporre la struttura dei prodotti in modo da individuare i gruppi che svolgono le stesse funzioni. Tali gruppi potrebbero essere in qualche caso uguali ma più facilmente sono solo simili, in quanto soddisfano funzioni uguali, ma con prestazioni diverse, per cui il progettista deve inserire parti o gruppi diversi per rispondere adeguatamente alle prestazioni richieste.
Per indagare ulteriormente sui gruppi simili, questi si possono scomporre in sottogruppi e così via:
Effettuata la scomposizione si possono analizzare le differenze e vedere se è possibile eliminarle creando nuovi gruppi che svolgono le funzioni richieste per tutti i prodotti, oppure utilizzare il gruppo più performante anche per i prodotti di prestazioni inferiori o ancora creare un sottogruppo base cui applicare parti o sottogruppi per ottenere la personalizzazione richiesta. Conviene fare prima un’analisi dello storico per decidere da quali gruppi partire per fare la riduzione delle varietà.
Nella tabella seguente per i tre prodotti della stessa famiglia sono stati identificati dei gruppi simili:
Prodotto 1 | Prodotto 2 | Prodotto3 | N° Tipi | |
Gruppo tipo A | A1 | A2 | A1 | 2 tipi diversi: A1 e A2 |
Gruppo tipo B | B1 | B1 | B2 | 2 tipi diversi: B1 e B2 |
Gruppo tipo C | C! | C2 | C3 | 3 tipi diversi: C1, C2 e C3 |
In ottica di diminuzione della varietà si dovrà indagare su più strade:
- È possibile creare un gruppo A3 che sia montabile su tutti e tre i prodotti?
- È possibile che il gruppo Ax, che è quello più performante, sia utilizzabile su tutti i prodotti?
- Se nessuna delle due strade è percorribile si può verificare se i due gruppi A sono scomponibili in due sottogruppi: uno comune ed uguale per entrambi che contiene la maggioranza dei particolari e due gruppi che gestiscono le differenze. Un tipico esempio è quello di due nastri trasportatori uguali come dimensioni, ma in cui cambiano le motorizzazioni: si può creare un gruppo nastro senza il motore e gestire due gruppi con ciascuna delle due motorizzazioni.
Tali analisi andranno sempre accompagnate da una valutazione costi, in quanto un aumento di costo del prodotto deve essere compensato in misura maggiore da un risparmio nei costi di gestione.
Diminuendo il numero di gruppi e/o parti si potranno anche ottener economie di scala e gestire una scorta a magazzino che permette di accelerare i tempi di produzione.
C –Le fasi del lavoro per la riduzione della varietà
Le fasi possono essere riepilogate nel seguente diagramma di flusso:
D – Il bilancio economico
Una volta ottenuta la riduzione delle varietà, si hanno dei benefici in termini, non solo di costo, ma anche in tempi di realizzazione dei prodotti e quindi saranno da rivedere le tabelle con i tempi di realizzazione del prodotto, facendo le opportune riduzioni in termini di ore. La riduzione dei costi di progettazione può variare fra il 25% e il 30%, mentre nei costi e tempi di produzione si può ottenere fino ad un 40%.
Articolo a cura di Alessandro Kokeny
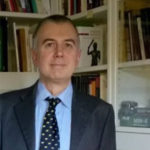
Alessandro Kokeny, laureato in ingegneria meccanica, ha conseguito una serie di certificazioni, tra cui: Black Belt Six Sigma, Lead Auditor Iso 14001, Agile Business Consortium, Scrum master Examination, Innovation Manager.
E’ stato inizialmente progettista meccanico in grandi Aziende del settore biomedicale, spaziando dalla progettazione meccanica all’integrazione hardware e software, fino a divenirne Direttore Tecnico. Dal 2015 è Consulente in CUBO dove svolge attività di Consulenza Direzionale ed Organizzativa e Formazione nel settore tecnico. Ha operato finora in oltre 80 Aziende.
Ha operato con gruppi di lavoro interfunzionali per introdurre AVP e Variety Reduction, FMEA e DFMEA, DOE, DTC, SIX SIGMA, TCM, ecc.