Impianti autocertificati. Il caso Tecnica Elettronica S.p.A.
Impianti Autocertificati
Nel suo sito, Tecnica Elettronica S.p.A., azienda veronese che progetta sistemi di programmazione e controllo di impianti automatizzati di produzione in diversi settori industriali, dichiara: “Ad oggi lo sviluppo qualitativo e quantitativo della Piattaforma TecnEl si muove per raggiungere l’obiettivo di impianto produttivo “autocertificato” in grado di fornire ad un generico stakeholder, abilitato e autorizzato a misurarne i comportamenti, tutte le informazioni necessarie per le valutazioni relative al grado di rispetto di normative vigenti o in corso di introduzione” [1].
L’azienda ha compiuto una scelta strategica significativa che:
- coglie alcune tendenze delle tecnologie I&CT (Information & Communication Technologies) e DCS (Distributed Control Systems) e la crescente necessità di misurare il comportamento degli impianti per rispondere a nuove esigenze di nuovi stakeholder, ad esempio dei sistemi HSSE (Health, Security, Safety, Environment);
- esprime l’interpretazione che l’azienda ha del ruolo del sistema di pianificazione e controllo come principale punto di passaggio delle informazioni da e verso l’impianto e sulla possibilità di trasformarlo in un sistema di raccolta di tutte le informazioni scambiate dall’impianto con i vari stakeholder. Ciò corrisponda ad una estensione delle funzioni del sistema;
- individua nella raccolta sistematica di informazioni una base per verificare e migliorare nel tempo le performance dell’impianto e per sviluppare nuovi servizi da fornire ai suoi clienti.
Sistemi di programmazione e controllo di impianti automatizzati
L’azienda in questione progetta e realizza sistemi di programmazione e controllo di impianti produttivi automatizzati in tre settori: Agroindustriale, Power Generation e Process&Factory. Cumulando le diverse esperienze maturate nei tre settori l’azienda ha acquisito conoscenze approfondite e strutturate su numerosi e diversi processi produttivi, continui e discreti, con parti automatizzate e parti non automatizzate integrate tra loro.
Un tipico sistema di programmazione e controllo realizzato di Tecnica Elettronica si articola in:
- interfacce con i sistemi gestionali aziendali dell’azienda che “ospita” l’impianto;
- interfacce operatore per la programmazione della produzione e il controllo di avanzamento;
- applicazioni e funzionalità MES (Manufacturing Execution System) con gestione ed elaborazione di informazioni per la supervisione del processo produttivo e l’integrazione con i sistemi di campo e ERP (Enterprise Resource Planning);
- sistemi PCS (Process Control System) per il controllo del processo: attuazione dei comandi, raccolta di informazioni dal campo, esecuzione delle operazioni automatizzate, gestione delle sequenze stabilite;
- infrastruttura elettrica per l’interfacciamento con gli equipaggiamenti di campo ed informatica per l’elaborazione e la distribuzione delle informazioni.
In Figura 1 è riportata la struttura funzionale di alto livello di un sistema di programmazione e controllo di un impianto produttivo automatizzato in cui si possono rintracciare i compiti delineati in precedenza.
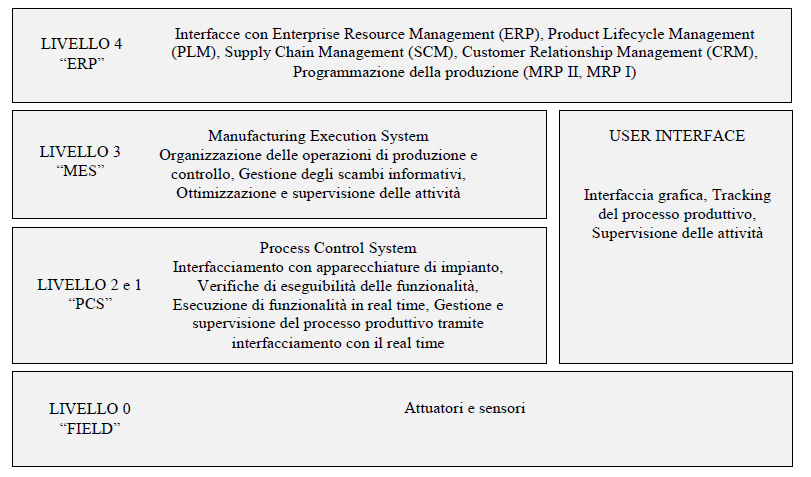
In Figura 2 è invece mostrata in modo semplificato la struttura fisica dove è possibile vedere il collegamento tra alcuni degli asset fisici e alcune delle funzioni svolte. La Figura 2 evidenzia quanto sia alta la compenetrazione tra sistema di programmazione e controllo e le altre funzioni “operative” dell’impianto di produzione. Alcuni sensori acquisiscono informazioni di estremo dettaglio, ad esempio se una pesatura è stata effettuata e con quale valore risultante o se una valvola di controllo è passata dalla posizione di riposo a una posizione attiva e se il controllo è stato positivo o, in casi più complessi, permettono il controllo di insiemi coordinati di operazioni in tempo reale.
Dalle Figure 1 e 2 è evidente che il sistema di programmazione e controllo è per sua natura e per le interconnessioni con le funzioni “operative” dell’impianto il principale collettore di informazioni sullo stato dell’impianto e sulle sue modifiche.
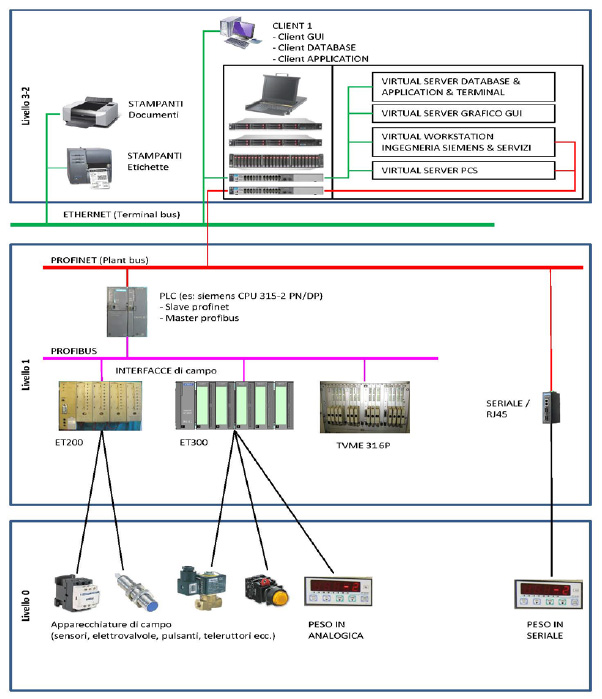
Impianti come fornitori di informazioni
In Figura 3, tratta da [2], è riportato uno schema molto generale delle principali classi di informazioni che un impianto è in grado di fornire a tutti gli stakeholder interessati al suo stato e al suo funzionamento. La Figura 3 non riporta, per semplicità, le informazioni che “vanno” verso l’impianto che riguardano sostanzialmente le ricette di produzione o le distinte base, il piano di produzione, le materie prime o, come si desume dalla Figura 2, i comandi da attuare.
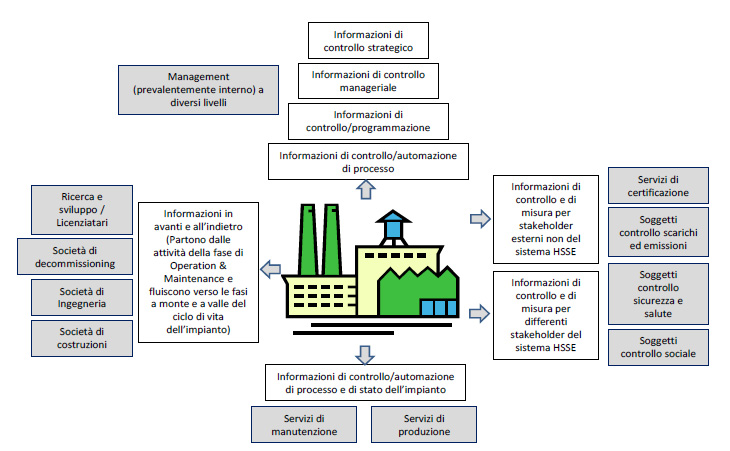
Alcune classi di informazioni servono al sistema di programmazione e controllo per “pilotare” l’impianto e i processi che in esso si svolgono. Gli stakeholder cui queste informazioni sono destinate sono raccolti, in Figura 3, sotto la voce Management.
Per garantire la qualità di questo flusso informativo, come visto, esiste una fitta rete di connessioni fisiche, stratificate su più livelli, che connettono specifici punti dell’impianto e il “luogo” in cui le informazioni vengono elaborate e tradotte in comandi per l’impianto secondo una logica che viene definita in fase di progettazione. Queste informazioni, nelle realizzazioni di Tecnica Elettronica, risiedono nei data base del sistema di programmazione e controllo e, in un secondo momento, sono trasferite, con opportuni trattamenti, nei data base aziendali.
Il trasferimento delle informazioni nei data base aziendali ha lo scopo di alimentare, insieme a quelle provenienti da altre fonti, tramite report o modelli di calcolo o altre procedure, quadri sintetici o analitici di indicatori che consentono di “misurare” il comportamento dell’impianto.
Un quadro sintetico di Key Performance Indicator (KPI) di alto livello per un processo produttivo è proposto in Figura 4 [3]. Si tratta di indicatori di grande generalità, usabili sia per processi a flusso, ripetitivi e standardizzati, che per processi a impulso, tipici dei progetti [4]. La determinazione di un parametro come la produttività si avvale sia di informazioni relative alle quantità prodotte e ai consumi di risorse, entrambe fornite dal sistema di programmazione e controllo, ma necessita anche di informazioni relative ai costi e ai prezzi, che spesso risiedono in sistemi informativi diversi[1].

Riquadro 1: Indicatori di misura della qualità dell’output
Qualità teorica: è un documento di valore contrattuale in cui sono elencate in modo il più possibile completo i parametri di performance dell’output, le modalità di misurazione e i range di eventuale tolleranza. E’ definita dalle specifiche. Di solito si distinguono le prestazioni fondamentali che qualificano l’output e quelle accessorie o opzionali. I parametri in cui si articola la qualità teorica dell’output di un impianto automatizzato di produzione sono essere molto numerosi, spesso articolati per funzioni svolte e per componenti che lo costituiscono.
Conformità: è il soddisfacimento dei requisiti fondamentali, cioè la rispondenza di ogni singolo output che viene prodotto alle specifiche di progetto (Uni En ISO 8402). Si distingue la conformità interna, cioè misurata prima della consegna al cliente da quella esterna, misurata sul campo, quando il cliente usufruisce dell’output. In genere nei settori in cui opera Tecnica Elettronica il riferimento sono disciplinari, leggi e norme riconosciute a livello internazionale. Le norme fanno riferimento sia al campo delle tecnologie informatiche che a quelle dei DCS (Distributed Control System)
Affidabilità: è l’attitudine di un oggetto ad adempiere alla funzione richiesta nelle condizioni fissate e per un periodo di tempo stabilito (Uni En ISO 8402).
Manutenibilità: è l’attitudine di un entità in assegnate condizioni d’uso a essere mantenuta o riportata in uno stato nel quale essa può svolgere la funzione richiesta, quando la manutenzione è svolta con procedure e mezzi prescritti (Uni 9910). In sostanza è la facilità di ripristinare il buon funzionamento a fronte di guasti o difetti
Servizio e assistenza; il servizio è il risultato di attività svolte all’interfaccia tra fornitore e cliente, per soddisfare le esigenze del cliente (Uni En ISO 8402). Il concetto di servizio comprende sia l’assistenza in senso stretto, sia gli aspetti legati alla consegna, sia gli elementi accessori alla transazione, quali ad esempio le condizioni della garanzia
Sempre in Figura 4, sotto la voce “Qualità dell’output” sono inseriti alcuni indicatori che stanno acquisendo sempre più importanza. Garantire che l’impianto produca un output conforme alle normative aziendali o a normative esterne o alle richieste di un cliente è una “responsabilità” del sistema di programmazione e controllo che definisce, esegue, controlla l’avanzamento e il completamento delle attività del processo produttivo e, che può divenire, con l’inserimento di opportuni strumenti di misura, il “certificatore” del valore degli indicatori di performance dell’output. La definizione di alcuni di questi indicatori è riportata nel Riquadro 1 in cui si evidenzia il ruolo centrale della “qualità teorica” come declaratoria delle caratteristiche e delle performance dell’output dell’impianto e, tramite gli indicatori di conformità e di affidabilità, si rende evidente la necessità di una misura che continua per tutto il ciclo di vita dell’impianto.
La funzione di raccogliere informazioni sull’output dell’impianto in modo continuativo, sistematico, adeguabile ad esigenze in evoluzione del management e dei clienti può essere assegnata, nel caso di impianti automatizzati di produzione, al sistema di programmazione e controllo come “estensione” di una funzione che esso già svolge e svolgerà per tutto il ciclo di vita dell’impianto.
Lo schema di Figura 4 è ottimo per la lettura e la classificazione delle performance operative di un processo/impianto di produzione, ma è possibile adottare schemi di più alto livello e di rilevanza strategica. Un esempio è quello proposto in [5], sintetizzato nella Balanced Scorecard, in cui l’impianto produttivo, o l’azienda, viene visto in un quadro economico, finanziario e di rapporto con il mercato.
Analoga riflessione si può fare per altre classi di informazioni contenute in Figura 3. Alcune servono al gestore dell’impianto come quelle inserite sotto le voci Servizi di Manutenzione e Servizi di Produzione altre servono a stakeholder esterni come quelle inserite sotto la voce HSSE. In [2] è presentata, a titolo di esempio, una classica tabella di misure per la valutazione dello stato delle acque reflue.
L’azienda, come del resto molte altre che progettano impianti[2], offre servizi di manutenzione, diagnosi ed assistenza a distanza che sono alimentati con informazioni definite da progettisti e fornitori, aggiornate in modo continuativo. Con il supporto di competenze e organizzazione e tecnologie di comunicazione, la differenza tra la manutenzione “di presenza” e quella “a distanza” tenderà a sparire. Se si comincia con ragione a parlare di diagnostica a distanza o di telemetria remota nel campo della medicina è possibile formulare questa ipotesi su sistemi meno complessi del corpo umano. Se i Servizi di Manutenzione potessero esplicitare compiutamente le loro esigenze informative in fase di progettazione dell’impianto, come fanno già attualmente i Servizi di Produzione in relazione alle operazioni da svolgere, e accedere a misure sistematiche e continuative, la qualità dei servizi di manutenzione, diagnosi e assistenza potrebbe alzarsi in modo considerevole. Un notevole miglioramento per i Servizi di manutenzione, verrebbe anche dalla possibilità di verificare sul campo modelli di affidabilità o di valutazione dei rischi che, basandosi sul concetto di probabilità di accadimento, potrebbero essere corroborati o migliorati sulla base di dati reali. Si aprirebbe la strada alla costruzione di modelli di previsione sempre più affinati e realistici. A questo miglioramento di prestazioni dei servizi potrebbe corrispondere una sensibile riduzione dei costi. In questa direzione spingono del resto metodi di miglioramento basati sulla misura, la raccolta di dati storici, la loro interpretazione tipici del Quality Management [7] e del Risk Management [8], [9].
Le Figure 3 e 4 e il Riquadro 1 mostrano, in definitiva, come sia possibile assegnare al sistema di programmazione e controllo di un impianto produttivo automatizzato la responsabilità di raccogliere informazioni che esulano del semplice controllo di processo o da una lettura del controllo di processo in senso stretto, finalizzata cioè alla conduzione delle attività, e che lo propongono come “centro di raccolta di tutte le misure eseguibili sull’impianto”.
Nuove funzioni del sistema di programmazione e controllo
Assegnare questa missione al sistema di programmazione e controllo è possibile e, sotto molti aspetti conveniente rispetto ad altre soluzioni, in quanto:
- il sistema di programmazione e controllo di impianti produttivi automatizzati ha una struttura fortemente decentrata, ramificata profondamente all’interno dell’impianto e dei suoi componenti, dotata di capacità di trasferimento, accumulo e trattamento delle informazioni. Per ottenere i flussi informativi di Figura 3 è necessario, nella maggior parte dei casi, semplicemente aggiungere al sistema di programmazione e controllo, nuovi apparati di misura e linee di connessione. E’ necessario inoltre introdurre procedure di misura e archiviazione adeguate alla destinazione e all’uso delle informazioni raccolte, e una robusta e qualificata interfaccia tra data base del sistema di programmazione e controllo e data base aziendali che è già una delle interfacce più importanti;
- la progettazione del sistema di programmazione e controllo e dell’impianto produttivo e, quindi, in specifico le sue performance e la loro evoluzione nel tempo, sono tra loro fortemente connesse e, spesso, contestuali. Con uno sforzo limitato si può estendere la progettazione delle “misure” anche a parametri non “convenzionali” richiesti da stakeholder terzi rispetto all’owner dell’impianto e al suo gestore o a stakeholder quali i Servizi di Manutenzione e Produzione;
- i sistemi di misura stanno sempre più elettronificandosi ed informatizzandosi, fenomeno che può essere fatto rientrare nella cosiddetta Internet of Things (IOT) ampiamente trattata in letteratura [10]; saranno perciò sempre più facilmente inseribili all’interno della rete del sistema di programmazione e controllo già profondamente distribuita all’interno dell’impianto. Probabilmente diverrà un problema la gestione di grandi moli di dati, ma i servizi di archiviazione, conservazione e reperimento di informazioni sono in rapido sviluppo [11];
- le misure effettuate nell’ambito del processo di programmazione e del controllo sono “certe e affidabili” in quanto sono quelle che hanno consentito di realizzare effettivamente le attività di produzione e controllarle. Programmare e controllare un dosaggio o una miscelazione richiede l’acquisizione e l’uso di informazioni certe e affidabili sulle quantità di materie prime e di output. Se queste informazioni vengono trasferite tramite procedure che garantiscono la “non manipolazione” successiva, si tratta di letture veritiere e aggiornate.
In Figura 5 sono schematizzate le funzioni dei sistemi di programmazione e controllo di impianti di produzione automatizzati che Tecnica Elettronica proporrà ai suoi clienti.
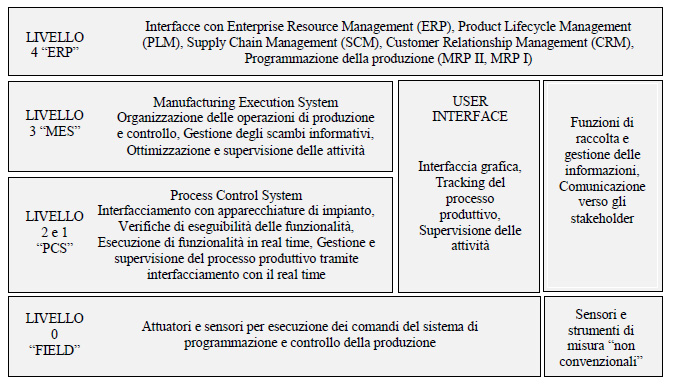
Verso nuovi sistemi di produzione
Gli impianti possono divenire autocertificati ampliando i compiti del sistema di programmazione e controllo sino a farlo diventare il punto di raccolta di tutte le “misure” sull’impianto. Tecnica Elettronica ritiene che impianti autocertificati possano dare un significativo contributo all’innovazione dei sistemi di produzione.
Dalla letteratura specialistica emerge uno scenario di evoluzione per i sistemi di produzione, automatizzati e non, che si articola intorno a tre principali tendenze.
- Il miglioramento delle performance dei processi aziendali. Esso è già oggi particolarmente attuale. Sempre maggiore è la diffusione di metodi BPR (Business Process Reengineering) applicati sia a processi di tipo amministrativo sia di tipo produttivo [12]. La possibilità di disporre dei valori delle performance di sistemi di produzione è in questo campo essenziale; la fase di misura dello stato attuale dei processi e dei sistemi tramite KPI e la definizione di quali migliorare è la base di partenza di qualunque intervento BPR.
- L’introduzione di nuovi metodi di produzione. All’orizzonte sono presenti numerose opportunità di innovazione. Si pensi alle stampanti 3D o a nuove tecnologie di lavorazione o ai nuovi materiali, alla diffusione delle tecnologie informatiche, alla diffusione dei device di comunicazione e misura. Tutte insieme queste opportunità stanno creando un’ondata di innovazione dei sistemi e dei processi di produzione che va sotto il termine Industry 4.0 [13] che originerà interventi di miglioramento di processi di produzione consolidati. Questa spinta, tra l’altro, coincide dal punto di vista temporale, con l’uscita da una crisi economica di dimensioni mondiali. Che le crisi siano un momento di profonda ristrutturazione dei sistemi, dei metodi e delle tecnologie di produzione è affermato da tempo da economisti di livello mondiale [14]. E’ quindi un momento in cui l’introduzione del concetto di impianto autocertificato può aiutare nella valutazione di investimenti complessi e onerosi. Solo misure e confronti di medio-lungo periodo diranno se questa ondata di innovazione si tradurrà in miglioramenti di performance e in investimenti remunerativi. Un punto rilevante del concetto di autocertificazione è, come già affermato, l’estensione della misura del comportamento sino alla fine del ciclo di vita dell’impianto.
- In [15], in una prospettiva storica e di lungo periodo, è proposto un modello interpretativo dello sviluppo dei sistemi produttivi che afferma come oggi e nel prossimo futuro il modello dominante sarà quello della “modularizzazione” e del “network produttivo” che ha l’obiettivo “non solo nella maggiore efficienza, flessibilità e innovatività, ma anche nella possibilità di variare la configurazione in modo da poter gestire qualsiasi opportunità di business provenga dal mercato del consumo”. Nell’articolo citato sono analizzati in dettaglio tre settori industriali: automobile, tessile-abbigliamento, agroindustriale, quest’ultimo di diretto interesse di Tecnica Elettronica.
Il concetto di network produttivo è già realtà nel settore della Power Generation. L’affermarsi di nuovi tipi di impianti produttivi, si pensi alle sorgenti rinnovabili, comincia a richiedere nuovi sistemi di programmazione della produzione in “real time” per tenere conto della dinamica della domanda di energia elettrica e delle caratteristiche della rete di produzione.
Le innovazioni di organizzazione, metodi e tecnologie evidenziate in [15] per il settore agroindustriale risaliranno certamente la filiera interessando in prima battuta i prodotti finiti e, successivamente i prodotti intermedi e quelli iniziali quali i mangimi o le attività di testa lasciando intravvedere un periodo di profonda innovazione.
Se la nuova organizzazione della produzione è quella del network produttivo c’è da attendersi lo sviluppo di sistemi di programmazione e controllo organizzati almeno a due livelli: quello della rete e quello del singolo impianto produttivo.
L’impianto di produzione automatizzato che nel passato e, in gran parte oggi, appare come un monolite isolato è destinato a diventare un nodo di una rete complessa. Essere il nodo di una rete richiede che l’impianto abbia precise caratteristiche di flessibilità, al mix, al volume e al prodotto e, soprattutto, abbia la capacità di comunicare in modo adeguato, certo e tempestivo, le propria disponibilità a produrre quanto richiesto. In relazione a queste esigenze, le risposte possono in parte venire dai sistemi di programmazione e controllo.
Per quanto riguarda la flessibilità occorre osservare che questa caratteristica è stata già nel passato oggetto di interventi. Nel settore Agroindustriale, ad esempio, l’azienda ha contribuito a realizzare impianti in grado di produrre prodotti con ricette diverse o in grado di modificare la ricetta nel corso delle attività produttive. Nel settore della Power Generation la flessibilità al volume è da sempre un parametro di progettazione. Lo sviluppo di impianti più flessibili richiede di rivedere in parte il ruolo dei sistemi di programmazione e controllo. Esso sarà ancora quello di ottimizzatore dell’uso delle risorse produttive e dei processi locali con una visione meno legata alla produttività e più legata alla flessibilità. Un ruolo rilevante che potrebbe essere assegnato al sistema di programmazione e controllo, tramite l’aggiunta di sensori e comandi opportuni, è quello di ridurre i costi fissi di produzione attraverso la riduzione degli sprechi. A titolo di esempio si possono citare i consumi di energia o di altre materie prime che potrebbero essere proporzionali ai volumi prodotti e quindi nulli quando l’impianto è fermo. In molti casi, già oggi, i componenti autoriducono i consumi in funzione dell’output, ma in altri casi occorre intervenire manualmente. Le esperienze nel settore della Domotica hanno dimostrato che è possibile una netta riduzione dei consumi con l’automazione di alcune procedure.
La capacità di comunicare tra il nodo della rete e sistemi sovraordinati è invece una caratteristica fondamentale degli impianti autocertificati. Essi possono dare il loro contributo in due modi:
- Centro di informazioni “veritiere” e in “real time” sullo stato dell’impianto e della sua attività produttiva. Si apre uno scenario di nuove informazioni da raccogliere e da trasferire in funzione del “modello” di decisione adottato al livello del network. E’ possibile che siano necessarie elaborazioni locali ad hoc per agevolare il compito del decisore;
- Simulatore di comportamento. In alcuni casi il sistema di programmazione e controllo locale sarà chiamato a “mostrare” come l’impianto è in grado di operare entrando in un modello di tipo “what if” che consenta di prevedere l’effetto di alcune scelte o di esplorare diverse alternative produttive.
Un impianto o una sua parte, come il sistema di programmazione e controllo, può essere progettato in maniera tale da fornire queste informazioni, talvolta in tempo reale, o “aperto” alla raccolta e fornitura di informazioni sul suo stato o sul suo comportamento una volta che l’obiettivo dell’autocertificazione sia assunto come una traiettoria di sviluppo o come, se si preferisce, una parte sistematica delle “specifiche”.
Nuovi servizi
In [16] è stata evidenziata la necessità di un ruolo di Information Manager in grado di svolgere tutte le funzioni legate alla gestione dei dati, dalla archiviazione alla manutenzione al recupero. Le funzioni sono riproposte nel Riquadro 2.
Riquadro 2: Ruolo dell’Information manager
L’Information Manager è colui che:
- dispone di metodi utili alle imprese o ad altri soggetti istituzionali per organizzare, recuperare, acquisire, assicurare e mantenere informazioni. Nel mantenere sono contenuti altri termini come creare, gestire, tracciare, modificare, revisionare, approvare, pubblicare e nel caso eliminare, documenti, informazioni, dati sia in forma cartacea che digitale;
- raccoglie e distribuisce le informazioni provenienti da una o più sorgenti e destinate a uno o più utilizzatori sulla base delle specifiche esigenze dei clienti/utilizzatori;
- assicura l’integrità dell’informazione anche a fronte di dinamiche di modifica elevate. Le modifiche vanno associate con il concetto di tempo e devono essere documentate;
- garantisce l’accesso ai documenti/informazioni sulla base di profili di autorizzazione rigorosi e rivedibili solo attraverso procedure concordate;
- nel caso siano adottati standard di rappresentazione delle informazioni, garantisce che le informazioni siano accessibili in qualunque momento indipendentemente dallo standard adottato. Analoga considerazione si può fare nel caso l’accesso alle informazioni preveda software specifici;
- elabora e mette in campo metodi e sistemi per fronteggiare le situazioni che possono danneggiare l’integrità delle informazioni;
- garantisce, attraverso l’uso di adeguati metodi e strumenti, livelli di servizio definiti contrattualmente e concorrenziali rispetto al mercato.
L’Information Manager è un ruolo che richiede un’attenzione particolare. Infatti:
- le informazioni sono ormai considerate un patrimonio strategico delle organizzazioni; d’altro canto diventano sempre più soggette ad usi impropri se non dolosi. Inoltre si stanno sempre più diffondendo software che consentono di interpretare e dare significato a grandi moli di dati elementari. La sicurezza informatica, concetto in cui sono compresi i requisiti di accessibilità, integrità, riservatezza, è ormai un imperativo categorico per le aziende [17]. Svolgere il ruolo di Information Manager in tutti i suoi aspetti richiede il possesso di un numero elevato di tecniche e di tecnologie. Basta focalizzare l’attenzione sul tema della sicurezza informativa e sulle norme ISO 27001 e seguenti, per avere un quadro più preciso. Il ruolo di Information Manager diventerà sempre più rilevante e sempre più difficile da svolgere;
- il ruolo è difficilmente “concentrabile” in una sola persona. Gli standard che descrivono le figure professionali usate nell’ambito delle I&CT [18] prevedono che i compiti previsti nel Riquadro 2 siano distribuiti tra le varie figure proposte. Inoltre il ruolo dell’Information Manager ha un contenuto organizzativo molto forte che difficilmente consentirà il suo “annegamento” all’interno della funzione che presidia l’I&CT. E’ interessante comunque il suggerimento di far svolgere il ruolo da un insieme di figure professionali in parte organizzative e in parte legate alle tecnologie che potrebbe far configurare il ruolo come un lavoro di team;
- lo sviluppo del Cloud Computing determinerà una crescita dell’outsourcing delle infrastrutture di I&CT in cui aziende di servizi informatici svolgeranno le attività più squisitamente tecnologiche previste nel Riquadro 1.
E’ quindi ipotizzabile che, salvo un presidio organizzativo interno alle aziende cliente, le attività del Riquadro 1 siano svolte da aziende di servizio specializzate con forti competenze nelle I&CT.
Questo ruolo potrebbe essere svolto anche da società di ingegneria quale Tecnica Elettronica che possiede le competenze necessarie per progettare e realizzare questo servizio, ma non dispone delle tecnologie e dei mezzi finanziari. La soluzione proponibile è quella della costituzione di reti di aziende di cui un componente disponga delle competenze e delle tecnologie adatte al ruolo[3]. In questo modo diviene possibile coprire tutte le attività relative ad un impianto autocertificato, dalla progettazione della rete di acquisizione delle informazioni alla loro gestione durante il ciclo di vita dell’impianto.
In [10], [13] e [15] viene proposto, anche se con modi diversi, il tema degli “oggetti”, siano essi sensori, apparecchiature, sistemi complessi quali i robot, in grado di interloquire con il mondo esterno scambiando informazioni, input e output, risorse e si utilizza molto spesso il termine “smart” per connotare questa caratteristica. E’ possibile affermare che il concetto di impianto autocertificato è molto simile anche se la base di partenza è diversa. Infatti, il concetto di autocertificazione nasce da idee legate alla qualità e alla gestione dei rischi, mentre quello di “smart object” è più legato all’innovazione tecnologica e, soprattutto dell’I&CT, ma il risultato tende ad assomigliarsi.
La differenza di fondo è che un impianto autocertificato risponde alle esigenze informative degli stakeholder durante il suo ciclo di vita, cfr. Figura 3, così come esse si esprimono in un determinato momento e come evolvono successivamente. Esso è pertanto progettato definendo funzioni e riducendo al minimo costi e tempi di realizzazione e adattato tramite progetti di revamping.
Lo studio e la realizzazione di progetti di revamping “funzionale” che hanno l’obiettivo di modificare il sistema di programmazione e controllo facendolo “passare” da quello espresso dalla Figura 1 a quello rappresentato in Figura 5 è uno dei servizi che Tecnica Elettronica intende proporre in prima battuta ai suoi clienti. Le conoscenze accumulate nel corso del tempo sugli impianti realizzati nel passato consentono di offrire questo servizio facendo compiere agli impianti un primo, rilevante, passo per inserirli nel nuovo mondo produttivo che si profila all’orizzonte.
Conclusioni
La direzione in cui Tecnica Elettronica intende muoversi nella progettazione e realizzazione di nuovi impianti automatizzati di produzione o nel revamping degli esistenti è quella dell’impianto autocertificato. La soluzione tecnica proposta è quella di una espansine delle funzioni del sistema di programmazione e controllo con le necessarie modifiche alle reti di acquisizione e gestione dei dati provenienti dall’impianto e al corredo di strumenti di elaborazione delle informazioni. L’interfaccia con i sistemi aziendali del cliente sarà una necessaria conseguenza.
Anche se il concetto di impianto autocertificato nasce dallo sviluppo dei concetti del quality management e del Risk management, esso appare convergente con le nuove filosofie, tecniche e tecnologie di produzione e informatiche che stanno emergendo a vario titolo, dall’Internet Of Things sino alla ristrutturazione in forma di reti di “nodi intelligenti” dei sistemi di produzione.
Infine l’azienda, percorrendo questa strada, pensa sia di migliorare in modo sensibile i servizi offerti ai clienti, dalla manutenzione a distanza sino alla diagnostica, e di attivare, anche con il contributo di partner qualificati, nuovi servizi sai nella gestione delle informazioni prodotte dagli impianti sia nella proposizione di revamping funzionali di impianti esistenti per portarli in uno stato adeguato agli scenari futuri.
Note
[1] Gli indicatori di performance di Figura 4 sono definiti in molti testi di management spesso corredati da modelli di calcolo o scomposizioni in parametri più semplici da rilevare ed elaborare.
[2] Un caso per tutti, molto citato, è quello del kit di teleassistenza di Sacmi [6]
[3] La scelta di costruire reti di azienda specializzate, “moduli” di un sistema produttivo, è abbastanza tipica del Veneto come testimonia l’esperienza dei numerosi distretti industriali. Nel caso specifico si fa riferimento alla rete Ager – Integrated Agrifeed Automation and Management che opera nel settore Agroindustriale (cfr. www.ager-network.com)
Bibliografia
- [1] www.tecnicaelettronica.it sito aziendale di Tecnica Elettronica S.p.A.
- [2] Bellucci A., Rossi M., Tunesi U., Plant Lifecycle Management – Autocertificazione dal mito alla realtà, Impiantistica Italiana, Gennaio – Febbraio 2015
- [3] Bartezzaghi E., Turco F., Indagine sull’applicabilità delle tecniche di gestione della produzione “Just in Time” alle piccole e medie imprese manifatturiere, Milano, 1990
- [4] Bellucci A., Colombo R., Opere pubbliche e Risk Management negli Enti Locali, Sviluppo & Organizzazione, n° 224, Novembre – Dicembre 2007
- [5] Kaplan, R. S., Norton, D. P., The Balanced Scorecard – Measures That Drive Performance, Harvard Business Review, January–February 1992
- [6] www.sacmi.it sito aziendale
- [7] Garvin D.A., Managing Quality, The Free Press, New York, 1988
- [8] CoSo (Committee of Sponsoring Organization of the Treadway Commission), La Gestione del rischio aziendale, Edizioni ilSole24ore, 2001
- [9] A Guide to the Project Management Body of Knowledge (PMBOK® Guide) 5th edition, Project Management Institute Inc., USA, 2013, chap. about Project Risk Management
- [10] Gubbi J., Buyya R., Marusic S., Palniswami M., Internet of Things (IoT): A vision, architectural elements, and future directions, Future Generation Computer Systems 29 (2013) 1645–1660
- [11] Mell P., Grance T., The NIST definition of Cloud computing, Recommendation of the National Institute of Standards and Technology, Special publication 800-145, September 2011. http://csrc.nist.gov/publications/nistpubs/800-145/SP800-145.pdf,
- [12] Bartezzaghi E., Dove va il BPR? Le prospettive dell’innovazione organizzativa basata sulle ICT, Mondo Digitale, n° 2, Giugno 2002
- [13] Brettel M., Friederichsen N., Keller M., Rosenberg M., How Virtualization, Decentralization and Network, Building Change the Manufacturing Landscape: An Industry 4.0 Perspective, World Academy of Science, Engineering and Technology International Journal of Mechanical, Aerospace, Industrial, Mechatronic and Manufacturing Engineering Vol:8, No:1, 2014
- [14] Schumpeter J. A., Teoria dello sviluppo economico, ETAS, Milano, 2002.
- [15] Massaroni E., De Falco E., Sancetta G., Cozzolino A., Bilotta A., Carrubotto L., Alla ricerca di un possibile principio evolutivo della teoria e della pratica d’impresa. Dinamiche di sviluppo delle modalità di produzione industriale, XXVI Convegno annuale di Sinergie Manifattura: quale futuro? Novembre 2014
- [16] Bellucci A., Plant Lifecycle Management – Opportunità per la costruzione di nuovi prodotti e servizi, Impiantistica Italiana, Gennaio – Febbraio 2014
- [17] Bellucci A., Beghelli F., Rossi M., Progettare sicurezza. Il caso Tecnica Elettronica S.p.A., in corso di pubblicazione, disponibile sul sito www.tecnicaelettronica.it
- [18 CNIPA, Dizionario dei profili di competenza per le professioni ICT. All’interno è citato anche il modello EUCIP, www.agid.gov.it
A cura di: Arturo Bellucci e Fabio Beghelli