Perché la misura dei tempi é tornata di “moda”?
INDUSTRIA 4.0: LA LEAN E LA MISURA DEI TEMPI
Premessa
Oggi tutti parlano e tentano di applicare i principi base connessi con INDUSTRIA 4.0, che principalmente richiedono di operare per processi continui, digitalizzati e automatizzati, anche con un largo utilizzo dei robots collaborativi.
Per ottenere questo obiettivo è opportuno, necessario applicare i principi della LEAN e la MISURA DEI TEMPI…
L’articolo vuole dimostrare come e perché oggi, più ancora di ieri, LA MISURA DEI TEMPI è necessaria per facilitare una corretta, efficace gestione dei processi aziendali, dopo aver eliminato gli sprechi con la LEAN, considerando sempre che il cliente “is the first”.
Un po’ di storia
IERI
L’Organizzazione tradizionale nell’Area Produzione si basa su un ufficio Metodi e un ufficio Analisi Tempi, i cui compiti sono di seguito riportati.
L’Ufficio Metodi e Attrezzature (detto anche ufficio engineering) ha il compito di studiare i cicli di fabbricazione/montaggio, suggerendo le attrezzature da utilizzare e/o da costruire ad hoc. Collabora con Ricerca & Sviluppo per migliorare i progetti per facilitarne la fabbricazione, evitando, ad esempio, che il progettista richieda tolleranze strette anche quando non servono o anche, invece di parti composte, uno stampato o una fusione.
In Giappone questo servizio è inserito nella R&S, in modo da fornire in tempo reale ai progettisti consigli perché ogni progetto sia più facilmente producibile, per non essere costretti a scegliere mezzi produttivi con elevate prestazioni, quando non necessario, o a introdurre solo successivamente modifiche, ritardando così i tempi di esecuzione.
L’ufficio Analisi tempi ha il compito di analizzare le operazioni, indicate sul ciclo studiato dai metodisti, e calcolarne il tempo necessario per eseguirle. Ha avuto una grande importanza fino a quando sono stati gestiti i cottimi, che, all’inizio degli anni 70, sono stati però soppressi. La soppressione dei cottimi ha ridotto, erroneamente, anche l’importanza della esatta, corretta misura dei tempi.
Per misurare i tempi, mediante cronometraggio o con le osservazioni istantanee, occorre suddividere le operazioni previste nel ciclo in attività elementari. I tempi sono calcolati per ognuna delle operazioni in cui è suddiviso il ciclo di lavorazione/montaggio, indicando velocità, avanzamenti, utensili da utilizzare in modo da avere un tempo che comprenda tutte le attività che ogni operatore deve eseguire dal prendere ad esempio il grezzo, posizionarlo sull’attrezzo, ecc. È valutata l’efficienza, cioè la velocità e la precisione di esecuzione, ed è calcolato il coefficiente di riposo, che tiene conto delle difficoltà per eseguire quell’operazione. Per poter definire un tempo corretto occorre eseguire almeno una decina di rilievi, con una durata minima per fase di 10/100 di minuto.
Rilevando i tempi per attività elementari era ed è possibile creare tabelle, per calcolare tempi senza doverli cronometrare.
OGGI
L’ufficio Metodi e attrezzature è ovviamente stato mantenuto, affidandogli gli stessi compiti e suggerendogli di valutare come utilizzare la digitalizzazione per uno scambio, ad esempio, di informazioni fra un centro di lavoro e il successivo, per rendere automatica la prosecuzione del processo, e di introdurre i robots collaborativi per assegnare loro le attività più semplici e ripetitive.
L’ufficio Analisi tempi è stato progressivamente marginalizzato perché si è preferito puntare sull’applicazione della LEAN.
La LEAN è una metodologia, importata dal Giappone, che ha per obiettivo principale la riorganizzazione dei reparti di produzione delle aziende.
La Lean postula la gestione delle Aziende per processi.
I processi vanno accuratamente mappati, creando una specie di PERT, che sarà suddivisibile in processi base e processi complementari, utili per facilitare il processo base. La gestione dei processi è affidata a gruppi interfunzionali empowerizzati, cioè che hanno le conoscenze e competenze necessarie per gestire autonomamente i processi loro affidati.
I gruppi operano come Circoli della Qualità, utilizzando i principi del miglioramento continuo per ricercare gli sprechi, introdurre i miglioramenti mano a mano si elimina uno spreco, poi ripartire per individuare altri sprechi: ogni soluzione migliorativa risulta così un punto di partenza. Eliminare uno spreco vuol dire ridurre i costi, che devono e sono tabellati e fatti conoscere a tutti compagni, colleghi e responsabili. Sono quindi estremamente utili per suggerire idee agli altri gruppi. Evidenziato uno spreco, il gruppo si riunisce per esaminare in brainstorming il problema, scrivendo tutte le proposte su post-it, attaccandole su un supporto idoneo. Successivamente il gruppo esaminerà le proposte una ad una, valutandone l’applicabilità e concordando, al termine dell’esame, il miglioramento da introdurre. Il miglioramento scelto è sempre accompagnato dai risparmi ottenibili, ad esempio in costi operativi, in materiali, in tempi di esecuzione, ecc.
I circoli della qualità sono ancora oggi molto diffusi in Giappone, perché fanno parte della loro cultura, nell’ottica di rispondere sempre all’obiettivo finale: il cliente “is the first”.
In Italia sono stati purtroppo abbandonati, perché dopo un primo periodo di introduzione, nel secolo scorso, durante il quale i gruppi erano guidati da consulenti o da dirigenti di alto livello, ottenendo risultati anche notevoli, furono trasferiti sotto la guida dei capi diretti, che per paura di essere scavalcati non portavano avanti i miglioramenti suggeriti dal gruppo o, addirittura, se li facevano propri. Il gruppo non ha più portato suggerimenti per non vederseli bloccare.
I gruppi interfunzionali continuano a gestire i processi ma non operano più come circoli della qualità.
Le direzioni di funzione
Operando per processi, le Direzioni di Funzione divengono punti di riferimento per i gruppi interfunzionali, dando loro assistenza per la risoluzione di casi anomali e stimoli per introdurre innovazione, suggerendo anche nuove vie. Le Direzioni non sono più quindi distributrici di attività, ma hanno assunto il compito di migliorare le conoscenze, le competenze e le capacità dei propri dipendenti. Concordano con il gruppo interfunzionale gli obiettivi e ne verificano il loro raggiungimento o meno per l’insorgere di cause non previste né prevedibili, che insieme saranno verificate e approfondite, per valutarne l’origine e come superarle.
I risultati
L’applicazione della Lean e il lavorare per processi hanno permesso di far emergere gli sprechi o le attività che non danno valore aggiunto, nel passaggio da una funzione alla successiva. Creando i processi, si sono così eliminate le barriere fra una direzione e l’altra.
Lavorare per processi ha evidenziato che la distribuzione dei compiti fra i componenti del processo non è né può essere omogenea, perché non si hanno a disposizione i tempi per le attività elementari che ciascuno dei componenti il gruppo deve svolgere né tanto meno si valuta l’efficienza dell’addetto che per eseguire certe fasi deve operare con una efficienza elevata mentre in altri casi può operare con un’efficienza normale.
In questo modo è stato evidenziato un problema di equità che deve essere risolto.
Il problema di equitá
I responsabili delle Aziende concordano che sicuramente l’applicazione della Lean dà vantaggi notevoli, quali:
- Eliminazione delle barriere fra una funzione e la successiva,
- Trasformazione dei compiti dei Responsabili di Funzione,
- Creazione di Gruppi Interfunzionali empowerizzati,
- Processi continui e ripetitivi,
- Ricerca ed eliminazione degli sprechi e/o delle attività senza valore aggiunto,
- Tempi di consegna ridotti,
- Costi più bassi,
- No magazzino, no work in process
ma anche svantaggi e cioè:
- una distribuzione dei compiti non omogenea,
- una intercambiabilità, dal punto di vista dell’impegno dei singoli, non sufficiente.
E questo succede perché i tempi delle singole attività di un processo non sono perfettamente noti, ma stimati con una certa approssimazione. Ne consegue che l’impegno richiesto per l’esecuzione dei vari compiti è diverso.
IL problema è ancora più evidente se vengono introdotti i Robots collaborativi: le attività loro affidate devono essere perfettamente definite, in modo che l’addetto possa integrarsi senza dispersioni o attese.
La LEAN non richiede di valutare l’efficienza, cioè la velocità e accuratezza che l’attività affidata richiede e inoltre manca la definizione dei coefficienti di riposo, che tengono conto della tipologia delle attività da svolgere, come difficoltà per movimentare le parti, la precisione, ecc.
La soluzione: La LEAN + La MISURA dei TEMPI
Molte Aziende oggi hanno ritenuto che è necessario avere una conoscenza sicura dei tempi. È stato richiesto l’intervento di consulenti in quanto in molte aziende l’ufficio tempi non esiste più o è a ranghi ridotti.
In molti casi le Aziende hanno richiesto adeguata assistenza per la sua rimessa in attività.
Per l’analisi tempi risulta fondamentale misurare i tempi necessari per eseguire una certa operazione, utilizzando la metodologia più idonea.
Si può ora affermare che LEAN per essere EFFICACE deve avere a disposizione i tempi delle attività che vengono svolte nei processi, per poter studiare una distribuzione dei compiti che tenga conto dei tempi effettivamente necessari e omogenizzi il carico di lavoro degli operativi.
La tabella per interventi efficaci
Nella tabella seguente, a fronte degli obiettivi, viene evidenziato come e quando utilizzare la LEAN e quando integrarla con la MISURA DEI TEMPI. La tabella evidenzia che in una riorganizzazione prima si introduce la LEAN che elimina gli sprechi e rende i processi continui e replicabili poi si misurano accuratamente le attività dei processi.
La tabella evidenzia che le due metodologie sono complementari, in quanto suggerisce che occorre suddividere l’azienda nei suoi processi, affidandone la gestione a Gruppi interfunzionali. Solo in questo modo:
- si introduce il principio che le Direzione di Funzione divengono propositrici di introdurre miglioramenti alle conoscenze e competenze degli addetti oltre che punti di riferimento per gli stessi,
- risulta più facile evidenziare eventuali sprechi,
- si fanno fluire in modo continuo materiali/informazioni perché è un gruppo interfunzionale che ne ha la responsabilità di gestione e ha l’obiettivo di eliminare le attività senza valore aggiunto per quel processo.
- stabilizzati i processi, risulta necessario procedere a misurare i tempi di tutte le attività.
- definiti i tempi è quindi possibile ricalcolare le attività in modo da poter eseguire una distribuzione che ne tenga conto,
- applicare i principi 5S per razionalizzare i posti di lavoro e facilitare l’esecuzione delle attività previste per ogni posto di lavoro,
- misurare i tempi con una delle tecniche indicate e comunque la più adatta per il processo da misurare:
- per attività continue si utilizza la cronotecnica completando i rilievi dei tempi delle fasi elementari con la stima dell’efficienza e del coefficiente di riposo,
Con i dati rilevati è possibile creare tabelle relative alle singole fasi elementari da utilizzare per calcolare i tempi relativi a nuove operazioni evitando così di eseguire nuovi rilievi cronotecnici, - per attività ripetitive ma discontinue, si utilizzano le osservazioni istantanee, che si basano su principi statistici, * in entrambi i casi i dati ottenuti permettono di ribilanciare la distribuzione dei compiti,
- per valutare attività nuove, per le quali non è possibile utilizzare la cronotecnica o le osservazioni istantanee, occorre prendere in considerazione le tabelle MTM UAS o anche quelle create con i tempi rilevati per attività assimilabili.
- per attività continue si utilizza la cronotecnica completando i rilievi dei tempi delle fasi elementari con la stima dell’efficienza e del coefficiente di riposo,
Conclusioni
Le esperienze fatte dall’Autore hanno dimostrato che l’applicazione della
LEAN + LA MISURA DEI TEMPI
hanno permesso di ottenere risultati migliorativi, che hanno prodotto una riduzione dei costi del 10/15%, oltre a quello ottenuto con l’applicazione della sola LEAN.
Articolo a cura di Gianni Cuppini
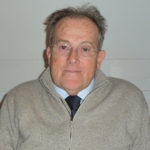
Gianni Cuppini, laureato in Ingegneria Elettrotecnica presso l’università di Bologna, è stato Dirigente del Servizio Organizzazione in una multinazionale americana per poi diventare Consulente direzionale prima presso la ORGA Srl di Milano poi alla CUBO Srl di Bologna di cui è tuttora Presidente. Ha operato in aziende italiane e multinazionali. Ha introdotto innovazione nei prodotti consulenziali. Ha pubblicato numerosi articoli su diverse testate italiane.