Ristrutturare la Supply Chain per la resilienza
Gli eventi provenienti dall’esterno, in particolare le crisi a carattere globale, possono essere per le imprese, oltre che minacce pericolose per la loro sopravvivenza, dei potenti acceleratori di innovazione.
Il contesto nel quale si opera può improvvisamente cambiare, come il COVID 19 sta mettendo in evidenza, per cause la cui natura ed origine può essere difficilmente o per niente prevedibile, o comunque non facilmente collocabile a priori nello spazio e nel tempo.
Seppure non siano prevedibili, è rilevante conoscere queste cause, innanzitutto per aiutare ad individuare indicatori premonitori di eventi analoghi, utili per il futuro.
E’ necessario comprendere le cause generatrici della discontinuità per individuare e parametrizzare gli indicatori sensibili più capaci di prefigurare gli scenari per eventi futuri analoghi, anche se rimangono eventi esogeni all’azienda, se non a tutta la sua Supply Chain di primo livello e successivi, sulla cui comparsa non si può incidere
Gli effetti, le conseguenze dirette e indirette, di questi perturbatori di equilibrio dell’intera Supply Chain Management, di processi consolidati con dinamiche note, possono però essere comunque prefigurati. Possono essere valutati gli impatti sull’azienda, preventivamente definite le azioni ed i processi per la loro gestione, a prescindere dalla causa che ha generato l’evento critico.
Conoscere le conseguenze dell’interruzione della Supply Chain, qual è l’anello più debole che l’ha provocata e qual è quello candidato ad innescare una futura interruzione, è importante perché da la possibilità di reagire e meglio ancora di attivare una gestione preventiva-predittiva delle crisi.
![]() | Il modello di Supply Chain Management efficiente, orientato alla massima riduzione dei costi, caratteristico ad esempio dei semiconduttori, concentra approvvigionamenti e trasformazione delle risorse a livello globale, la distribuzione con modello hub, lasciando i soli canali di distribuzione finale a livello macro-continentale. La forte dipendenza della Supply Chain dalla concentrazione delle capacità e di allocazione delle risorse la rende fragile ed esposta ad elevato rischio di interruzione. |
La crisi per la pandemia che ha provocato l’indebolimento se non l’interruzione della Supply Chain praticamente in tutti i settori imponendo di ripensare la strategia, i modelli: paradossalmente gli effetti sono stati più rilevanti nelle filiere e nei settori con una Supply Chain più efficiente.
Un esempio di interruzione di Supply Chain constatato da tutti è stata la crisi delle mascherine, per la protezione delle vie respiratorie, i dispositivi di più semplice contenuto tecnologico, quali le “mascherine mediche” o più complesse come le FFP2, che rispetto alle altre hanno requisiti tecnici più stringenti per garantire la protezione, con parametri definiti, del portatore (protezione in ingresso).
La Supply Chain per le due tipologie, sotto schematizzata, non è molto diversa se non per le tecnologie del manufacturing, potendosi realizzare le forme delle FFP2 con termoformatura, invece che con tranciatura-saldatura per ultrasuoni.
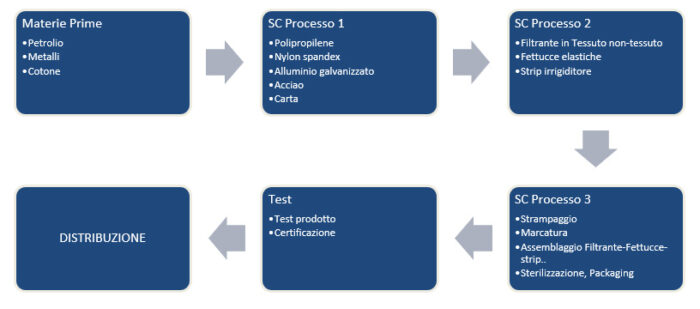
La Supply Chain delle mascherine è andata immediatamente in crisi interrompendosi per effetto dell’enorme aumento della domanda: il principale produttore che è la Cina passò da una domanda totale interna ad inizio crisi di 20 milioni/giorno che era capace di soddisfare in totale autonomia, ad un fabbisogno stimato di 240 milioni/giorno necessarie per soddisfare solo la domanda interna di personale più critico (sanitario, trasporti e parte manifatturiero). L’interruzione della Supply Chain e la crisi conseguente, per mancanza di capacità produttiva a livello globale, è stata solo in minima parte attenuata dal commercio internazionale.
Fattori di criticità globale della Supply Chain mascherine al momento della crisi:
- Concentrazione della quasi totalità della Supply Chain e delle capacità produttiva in un unico paese (Cina)
- Oligopolio nei semilavorati: Il polipropilene (PP) utilizzato per la produzione del TNT filtrante melt-blown è fornito da pochi produttori al mondo, per tutti i settori di utilizzo, che hanno rapidamente saturato la loro capacità produttiva
- Il processo di formatura, sia per ultrasuoni che per termoformatura, è specifico per le mascherine, seppure utilizzato in molti altri settori richiede tempo per la riconversione degli impianti
- La distribuzione si è dovuta adeguare al numero crescente di limitazioni e/o divieti governativi di esportazioni, oltre che ai rallentamenti del commercio globale per effetto del covid-19
Fattori critici nazionali, ad esempio in Italia a livello nazionale, si sono aggiunti localmente a quelli globali:
- La SC esistente copriva, per i fabbisogni pre-crisi, la sola fase di distribuzione locale, dipendendo per tutto il resto da distributori globali, produttori esteri di semilavorati, prodotti finiti e fornitori di materie prime
- Non c’erano strutture, tecnologie pronte e processi testati, non il know how per la produzione delle mascherine
- Per le fasi di test del prodotto laboratori certificati erano 17, ma notificati e quindi autorizzati per le prove e la successiva certificazione a marchio CE (come previsto per mascherine FFP2) c’era un solo laboratorio. C’era un solo organismo notificato per la certificazione dei test dei laboratori riconosciuto dall’EU.
Conoscere le conseguenze dell’interruzione della Supply Chain e di quale anello l’ha provocata è importante, perché dà la possibilità di reagire ed ancora meglio di mettere in condizione di poterne fare una gestione preventiva e predittiva. Nel caso delle mascherine il primo anello a cedere è stato quello del manufacturing, la trasformazione delle risorse, subito dopo gli altri. A livello nazionale anche quello della distribuzione.
Più in generale le crisi suggeriscono o impongono, pena la continuità delle aziende, di ristrutturare la SC, innovandola: è un processo che richiede la revisione delle strategie e di paradigmi consolidati da cui evolvere.
L’agilità della Supply Chain è il requisito necessario, cioè la capacità di gestire gli effetti di eventi di crisi e si misura attraverso la sua “Resilienza”, la prova che in ingegneristica testa la resistenza agli urti senza fenomeni di rottura, rende bene l’idea delle caratteristiche peculiari da perseguire e rinforzare.
Ripensare la Supply Chain Management, che non è certo soltanto la gestione della propria catena di approvvigionamento, ma la più ampia ed articolata capacità di gestione dei flussi e delle interazioni tra le catene di Supply Chain e di Operations di diversi livelli, tra loro correlate. Nei sistemi complessi operano decine di Supply Chain, di diverso livello, che coinvolgono direttamente o indirettamente molteplici aziende che quindi condividono rischi ed opportunità: contesto di cui bisogna essere consapevoli e conseguenti.
Quindi, sottoporre la SCM a stress-test preventivo con la valutazione strutturale del fattore rischio per la gestione degli effetti connessi e per contribuire, con gli altri anelli, a far evolvere la propria SC verso l’agilità.
In questa direzione diversi paradigmi devono essere rivalutati, dove necessario si devono individuare i fattori critici con i relativi trade-off, quali ad esempio:
- Globalizzazione e Localizzazione
- Outsourcing ed Insourcing
- Make or Buy
- Efficienza ed Efficacia
Ristrutturare quindi la SC perché diventi agile, evoluzione più impegnativa dei modelli efficiente e reattiva, con l’obiettivo di preservare i loro punti di forza, grazie all’utilizzo adeguato delle molte leve disponibili, non solo tecnologiche.
Note
OECD – The Organisation for Economic Co-operation and Development www.stats.oecd.org/
WTO – World trade organization www.wto.org/
“Operations and process management. Principles for strategic impact” N.Slack ; A.Brandon-Jones Ed.: Pearson Education Limited
Articolo a cura di Francesco Liguori
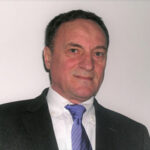
Francesco Liguori, laureato nel 1986 in Ingegneria navalmeccanica all’ Università degli studi Federico II di Napoli.
Dopo il programma “Production, Planning&Control” (Imperial College – Cranfield Institute - UK), per 16 anni ha svolto attività in aziende internazionali (Fincantieri e KME) presidiando le diverse funzioni delle Operations quali Project Manager, Ufficio Tecnico, Tecnologie, Produzione, Pianificazione e Controllo.
Dal 2004 è Temporary Manager, partner di Cdi Manager e Consulente di Management qualificato APCO CMC, certificazione internazionale ICMCI dal 2010. CV validato con assessment di Niederdorf Italia nel 2020.
Ha svolto incarichi di cambiamento organizzativo in PMI di settori diversificati nell’ambito di strategia ed operations, nelle diverse fasi sia di crescita che di ristrutturazioni, realizzando obiettivi di efficienza dei processi ed efficacia organizzativa, valorizzando le risorse disponibili ed apportando positive contaminazioni di best practice/competenze tra settori diversi.
Come esperto di operations collabora dal 2010 nell’ambito della formazione superiore per professionisti e responsabili aziendali di funzioni.